Sheet Metal Enclosure Design
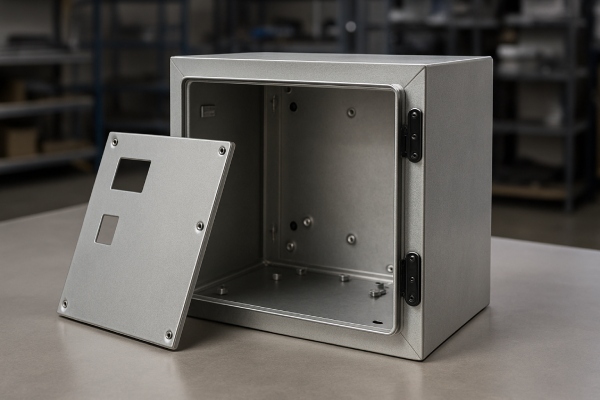
- Introduction
- Key Takeaways
- The Carbon Steel Material Family
- What is Important for Sheet Metal Enclosure Design?
- Selecting the Right Sheet Metal Material
- Key Design Considerations for Sheet Metal Enclosures
- Waterproofing and Sealing
- Heat Dissipation and Ventilation Strategies
- Surface Finishing and Corrosion Protection
- Design for Manufacturability and Cost Optimization
- Testing and Validation of Sheet Metal Enclosures
- Ensuring Compliance with Industry Standards
- Prototyping & Design Reviews
- Conclusion
Introduction
Sheet metal enclosures are casings made from fabricated metal sheets for protecting, shielding, and mounting electrical components. They play a vital role in safeguarding electronic and mechanical systems by protecting against physical damage, thermal changes, and electromagnetic interference.
Poor enclosure design can create heat management issues, increase system cost, and complicate waterproofing and component mounting. To help guide you through the considerations and steps to designing a sheet metal enclosure, we’ve created a simple walkthrough on how to weigh the various choices and tradeoffs involved.
Key Takeaways
- The first step in enclosure design is to consider the operating environment and application requirements (temperature, corrosion and impact resistance, sealing).
- Material and finishing choices should align with those application needs.
- Waterproofing and sealing are essential for protecting internal components.
- Robust thermal management can be achieved through aluminum enclosures, venting, or other active and passive cooling structures.
Table of Contents
- Introduction
- Key Takeaways
- The Carbon Steel Material Family
- What is Important for Sheet Metal Enclosure Design?
- Selecting the Right Sheet Metal Material
- Key Design Considerations for Sheet Metal Enclosures
- Waterproofing and Sealing
- Heat Dissipation and Ventilation Strategies
- Surface Finishing and Corrosion Protection
- Design for Manufacturability and Cost Optimization
- Testing and Validation of Sheet Metal Enclosures
- Ensuring Compliance with Industry Standards
- Prototyping & Design Reviews
- Conclusion
What is Important for Sheet Metal Enclosure Design?
A sheet metal enclosure is a protective housing made from metal sheets designed to safeguard electronic and other vital components. The key factors in its design are the following:
Form Factor and Design Meets Application Needs
- Try to minimize the enclosure’s size by considering how to stack internal components without wasting space, all while allowing for adequate airflow and thermal management.
- Component spacing is particularly important if including parts that generate significant heat (e.g. power supplies or boards), even if there is active cooling in the enclosure.
- Impact resistance and overall strength are equally vital, as the enclosure must endure mechanical stresses and shocks during both installation and operation.
Simplify Assembly & Service
- The enclosure should allow for the straightforward installation of primary components from the doorway
- This means easy access for any screw points or fasteners, and clear view of all components
- Simplifying assembly also helps to simplify service or rework in the field – it’s worth taking the time to optimize.
- Consider mounting points for components and cable routing
Cost Effective & Straightforward to Manufacture
- A good enclosure design must strike a balance between performance and manufacturing efficiency.
- A cost-effective design reduces production complexity – this often means minimizing welding as much as possible
- Welding is expensive and requires secondary processing (grinding, polishing, etc.) – try to minimize as much as possible
- CNC bending is a useful tool to combine parts and minimize part count
Environmental Factors
- It’s important to consider what kind of water or weather the enclosure will need to hold up to: rain, power washing, snow, salt exposure, UV exposure, etc.
- Corrosion and weather resistance can come from material selection (stainless / aluminum / UV-resistant plastics) or by secondary finishing (powder coating, galvanization, etc.).
- The harsher the environment, the more thought and expense is needed to design an enclosure that can hold up well without constant maintenance or replacement parts.
Key Performance Factors Factors
- Adequate strength guarantees that the enclosure can absorb physical shocks
- Efficient heat dissipation prevents overheating, thereby extending the lifespan of the internal components.
- Incorporating EMI shielding within the design is crucial to avoid electromagnetic interference affecting the enclosed electronics or to control emitted radiation to comply with EMC standards
Effective Grounding
- Most enclosures will require some type of electrical grounding in order to be certified for CE, ETL, UL, or other standards.
- This generally means having a grounding point (usually near the power supply entry) and incorporating grounding lines with lock washers and nuts to the various energized components or surfaces
Selecting the Right Sheet Metal Material
Selecting the right sheet metal material is essential in designing an effective enclosure. Here are some commonly used materials for manufacturing enclosures:
- Cold Rolled Steel: a common choice due to its low material cost and reasonable strength, as well as ease of fabrication; this will require secondary finishing to prevent corrosion.
- Stainless Steel: It provides superior strength and natural corrosion resistance, making it highly suitable for harsh environmental conditions. Secondary finishing is not necessarily required, but the material cost is about 5x carbon steel, so it is usually selected only for the harshest environments.
- Aluminum: It is lightweight and has a natural ability to resist corrosion, alongside excellent heat dissipation properties – meaning enclosures made of aluminum often don’t require active cooling, which can bring down design complexity and cost. Its relatively high material cost and susceptibility to bending, scratching and other physical, however, can limit its use in applications demanding greater strength.
- Galvanized Steel: With its pre-applied rust protection, it offers a practical and economical solution for outdoor applications. It minimizes the need for secondary processing, although the integrity of its protective coating can be compromised if the material is cut or bent.
- Titanium: Though it is expensive, it is used in aerospace applications because it is light, has high strength and excellent corrosion resistance.
Key Design Considerations for Sheet Metal Enclosures
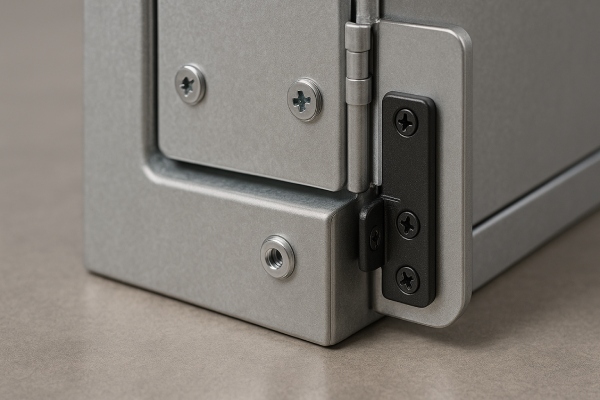
Bending and Forming
- In the design of sheet metal enclosures, the bend radius is crucial because it directly affects the strength of the structure.
- When the metal is bent, a gradual curve can help distribute stress evenly, whereas too-tight bends or sharp corners may weaken the enclosure and create potential failure points.
Fastening and Assembly
- The efficiency of the assembly process depends on the chosen fastening methods.
- Whether employing traditional screws, press fit nuts, cage nuts, etc., the goal is to have straightforward assembly (which means enough room and clear access for tools).
- Incorporating PEM inserts can further allow improved assembly efficiency and reduce the risk of misalignment.
Hinges and Access Panels
- Ease of maintenance plays a vital role in an enclosure's long-term performance, which is why designing with accessible hinges and access panels is essential.
- Technicians will often need to perform routine inspections and repairs without having to dismantle the entire enclosure.
Waterproofing and Sealing
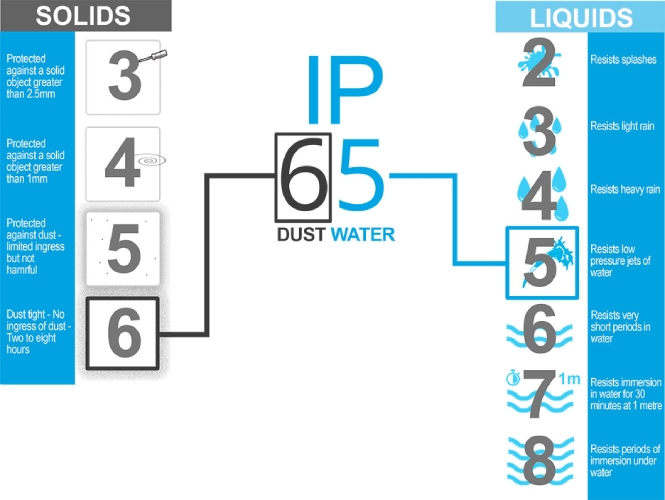
Waterproofing and sealing enclosures is an essential part of protecting sensitive electronic components; this is why there are a number of standards and ratings which evaluate the sealing performance of an enclosure.
- NEMA classifications provide criteria for assessing an enclosure’s ability to withstand environmental challenges such as water, dust, and even temporary submersion, with a focus on practical performance in industrial and outdoor settings.
- The IEC IP rating system, developed by the International Electrotechnical Commission, offers a detailed two-digit code that defines protection levels against the ingress of both solid particles and liquids.
- UL standards set rigorous benchmarks for safety and performance, ensuring that enclosures not only meet protection requirements but also conform to strict industry safety protocols.
Integrating these diverse standards—NEMA for broader environmental resistance, IEC IP for detailed ingress protection, and UL for comprehensive safety—guides engineers in developing robust enclosures that offer reliable, long-lasting protection in even the harshest conditions.
Heat Dissipation and Ventilation Strategies
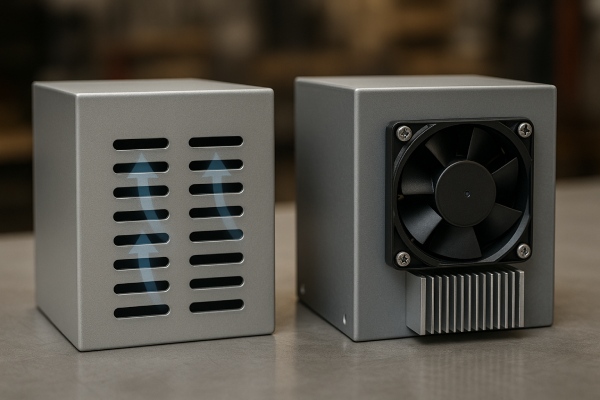
The Importance of Airflow in Electronic Enclosures
- Adequate airflow is essential for dissipating heat generated in the enclosure.
- This will prevent thermal buildup, which can lead to performance degradation of the installed components.
- Designing for optimal airflow is not simply the placement of vents and openings but also understanding the internal layout of components to ensure that warm air is removed and replaced by cooler air.
Designing Ventilation Slots vs. Using Active Cooling
- Passive Cooling
- Adding ventilation slots in an enclosure is a passive approach to cooling that utilizes natural convection air currents.
- When these slots are appropriately sized and strategically placed, they allow heat to escape naturally.
- There are downsides here, in that any opening in an enclosure can increase exposure to external humidity, so vent location, size, and potential protection need to be considered carefully.
- The use of aluminum as an enclosure material is another form of passive cooling – aluminum allows for much more rapid heat dissipation vs steel or plastic enclosures.
- Active Cooling
- Incorporating active cooling components such as fans and heat sinks, a more controlled cooling environment is achieved by forcing air over critical components and generally has reduced impact on weather resistance.
- This comes with some increased complexity in terms of wiring and assembly, as well as higher energy consumption and issues such as fan failure or added noise.
Managing Thermal Expansion in High-Temperature Environments
- Managing thermal expansion is crucial to maintaining both the physical integrity and the thermal performance of the enclosure.
- You must consider material properties and design features that allow for controlled expansion and contraction. This might involve incorporating flexible joints, using materials with similar thermal expansion coefficients, or designing tolerances that can accommodate slight dimensional changes.
Surface Finishing and Corrosion Protection
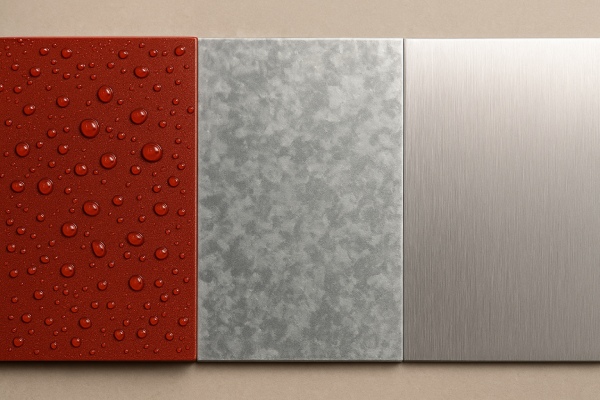
Surface treatments are integral to extending the life and performance of sheet metal enclosures. Here are some common surface finishes:
- Powder Coating: A process that provides a durable and attractive finish, enhancing both aesthetics and resistance to environmental wear.
- Anodizing: Primarily used for aluminum enclosures, this treatment creates a hardened oxide layer that improves corrosion resistance while allowing for decorative color options.
- Galvanization: Involves applying a zinc coating to steel surfaces to protect against rust, offering a cost-effective solution for outdoor and corrosive environments.
Choosing the Right Finish Based on Application
- Outdoor Applications
- Powder coating and hot galvanization are preferred for outdoor enclosures because they deliver enhanced protection against moisture, UV exposure, and other environmental challenges.
- Hot galvanization also offers excellent corrosion and wear protection, though it can deform thin sheet metal.
- Grounding - powder coating serves to prevent electrical conductivity (powder coating is plastic and non-conductive); this isn’t enough for full grounding protection but is a good option.
- Electrical Conduction - Anodized aluminum surfaces offer good corrosion resistance while maintaining conductivity for effective grounding and electromagnetic compatibility.
Design for Manufacturability and Cost Optimization
Reducing the Number of Parts for Simplified Assembly
- Designing with manufacturability in mind means beginning with a reduction in the number of individual parts.
- Fewer parts means less complexity, easier and faster assembly and service, and usually lower costs.
Standardizing Components to Lower Production Costs
- Off the shelf parts are most cost effective, easier to purchaser, and available in low to high quantities.
- Custom parts should be avoided in most cases if there are good options available – there are generally MOQ, cost and tooling considerations.
- That said, Asian supply chains can offer fairly low-cost custom components if the design really calls for it.
Pick the Right Process for the Right Volumes
- CNC Machining – this generally a last resort; CNC machining is extremely expensive and time-consuming; some components cannot be made precise enough otherwise, but a general rule is to avoid unless very low volumes are involved.
- Laser Cutting & CNC Bending – these processes allow for very flexible production; anywhere from single parts to thousands of enclosures can be made at relatively low costs, and with zero or minimal tooling.
- Stamping – stamping is usually selected only when the order volumes are in the mid-thousands per production; depending on enclosure size, tooling costs can scale rapidly, so only very high volume projects will generally be stamped.
Testing and Validation of Sheet Metal Enclosures
Drop Tests, Vibration Tests, and Environmental Stress Testing
- Enclosures are routinely put through drop tests to simulate accidental impacts, ensuring that any shock encountered during handling or deployment does not compromise their integrity.
- Vibration tests further replicate the conditions experienced during transportation or operation in dynamic environments.
- Environmental stress testing exposes the enclosure to temperature fluctuations, humidity, and corrosive conditions to verify that the materials and seals can withstand the demands of real-world applications
- Salt spray testing – tests corrosion resistance of base material and finishing
- IP rating testing – evaluates waterproof or water resistance of enclosures
Ensuring Compliance with Industry Standards
Enclosure certification is usually highly, highly market and industry specific. A single sheet metal design might be able to be used across multiple industries, and even though the design is the same, testing standards might be different for each individual industry. Usually, this is why consulting with a 3rd party testing laboratory like Intertek, UL, SGS or others is so useful. There are a lot of potentially applicable standards – the best approach is to work with a company that can help you interpret which actually DO apply.
A complicating factor is that many of these organizations or groups can have their own, company-specific certification (UL, CSA, NEMA, etc.), which can sometimes stand in as the national certification standard.
One final aspect is that certification can be aimed at different aspects of the enclosure performance: electrical safety, ingress protection, EMI shielding or EMC compatibility, etc. We’ve listed some of the most commonly referred to standards.
UL Standards (Underwriters Laboratories) – US market
- UL 50 / UL 50E: enclosures for electrical equipment
- UL 508A: industrial control panels and associated enclosures
CSA Standards (Canada)
- CSA C22.2 No. 94.1 / 94.2: - this is more or less equivalent to UL 50 standards for enclosures.
Water Resistance
- IEC 60529 standard for ingress protection (IP ratings)
- NEMA IP rating certification
Application-Specific Certifications
- ATEX / IECEx: Required for enclosures used in explosive atmospheres (e.g., oil & gas)
- MIL-STD-461 – military EMI enclosure rating
- Automotive – ISO 16750
Prototyping & Design Reviews
Before committing to mass production, developing and testing prototypes is a critical step in the validation process. Prototyping allows you to evaluate the practicality of the designs under simulated operational conditions, highlighting any potential issues in material selection, assembly, component fit, or thermal management.
Prototype Production
Generally, the best approach is to use laser cutting, CNC bending, punching and other non-tooled processes to first test and evaluate the assembly and overall design of your enclosure. Stamping tools are relatively fragile due to the force applied to them, so repeated changes can damage the tool or even destroy it. Rapid prototyping through laser cutting, 3D printing and other processes not requiring tooling is the way to go.
Prototype Quantity
It’s almost always best to produce several units at once, and modify as needed, than to produce single units, purely for batch cost reasons. If you are doing field testing, multiple units are needed for a more representative performance or analysis. The same is true of certification.
Conclusion
The key design principles for sheet metal enclosures emphasize a harmonious blend of functionality, durability, and cost-effectiveness. You must consider material selection, ensuring that the chosen metal not only meets structural and thermal requirements but also endures environmental challenges through proper surface treatments. Equally important is the focus on manufacturing efficiency and optimizing material usage. Finally, ensure robust performance through rigorous testing.
Have questions about your enclosure design? Contact us today for personalized guidance from our manufacturing experts.