- Determine the Best Packaging
- Shipping Methods
- Bulk Shipping
- Knocked-Down Assemblies
- Assembled Part Packaging
- Distribution Methods
- Logistic Costs Calculation
- Product Packaging
- Packaging Carton Options
- Internal Packaging Materials
- Corrosion Protection
Packaging and Shipping Best Practices for Sheet Metal Fabricated Parts
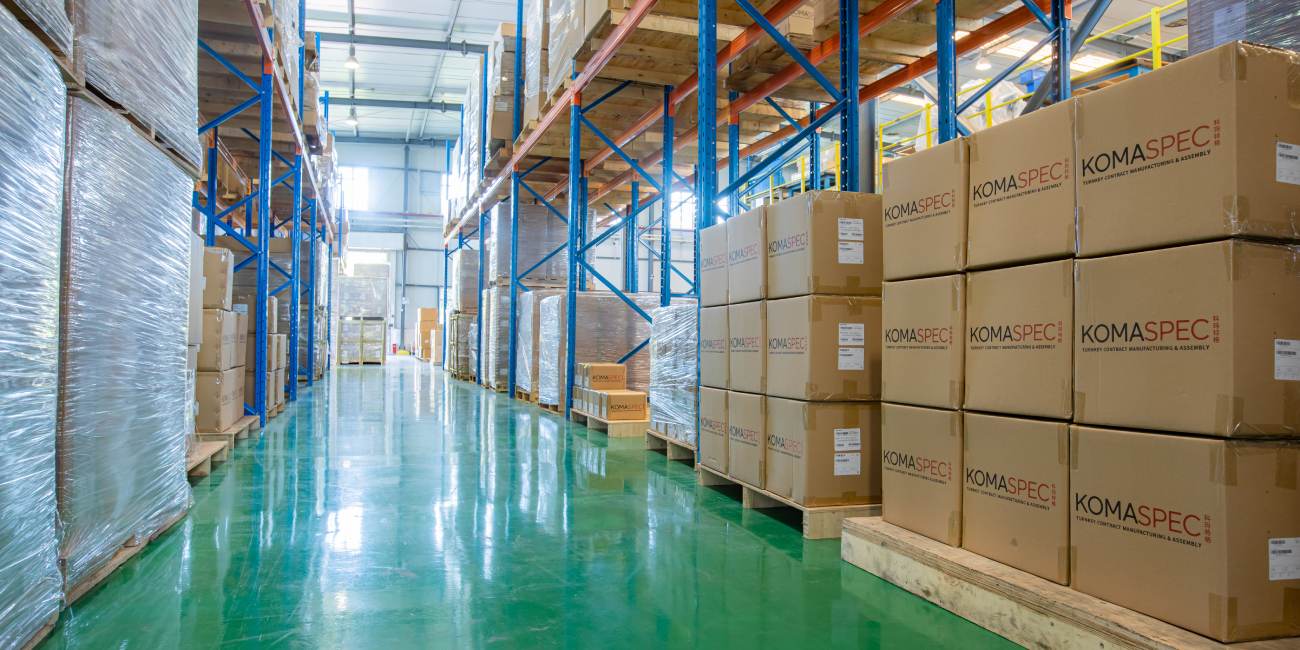
Table of Contents
- How to Determine the Best Packaging for Sheet Metal Parts and Assemblies
- Shipping Methods for Sheet Metal Products
- Bulk Shipping Sheet Metal Parts
- Knocked-Down Sheet Metal Assemblies
- Assembled Sheet Metal Part Packaging
- Distribution Methods
- Calculate Preliminary Logistic Costs
- Designing and Engineering Sheet Metal Product Packaging
- Packaging Carton Options
- Internal Packaging Materials
- Corrosion Protection During Shipping
How to Determine the Best Packaging for Sheet Metal Parts and Assemblies
A lot of work goes into partnering with a custom fabricator to manufacture quality sheet metal parts and assemblies. So, you want to be sure that after production is finished and the goods are sent, they arrive undamaged and ready for use.
It’s always a good idea to do some research and speak with your manufacturer to make sure your goods are shipped in the right packaging. A good sheet metal fabricator will also want products to arrive in perfect condition as much as you do to avoid returns and quality issues. They should try to accommodate any reasonable packaging demands you make and help you to not only find the right packaging, but also a cost-effective way of providing it for you.
A good way to look at packaging design is to consider it as an important part of the sheet metal production process. There’s no point creating high quality parts and assemblies only to have them damaged during transit or arrive in an unpresentable way. Packaging design should take into consideration the entire logistics cycle, shipping requirements and the material and geometry of the sheet metal parts themselves.
There’s lots to think about when it comes to packaging sheet metal products for shipping. In this guide, we’ll cover the primary factors that influence packaging design and the different packaging types that are available.
Shipping Methods for Sheet Metal Products
Before you start thinking about how to design packaging for your parts, you should think about how you will be shipping those parts.
- Are you shipping parts packed in bulk, or individually?
- Are you sending sets of components to be assembled later in kits?
- Are you shipping sheet metal assemblies fully assembled or knocked down for assembly at the end customer side?
All of these scenarios will impact how you think about your sheet metal product packaging. The main factors to consider are:
- Cost savings associated with closely packed deliveries
- What assembly procedures can be carried out after delivery
- Other logistical considerations in the shipping process
Here are some of the use cases as well as the pros and cons of bulk shipments, knock down shipments and fully assembled deliveries.
Bulk | Knocked Down | Assembled | |
---|---|---|---|
When |
|
|
|
Pros |
|
|
|
Cons |
|
|
|
Bulk Shipping Sheet Metal Parts
When bulk deliveries of parts are shipped, the most economical way to approach packaging design is to pack the parts as close together as possible.
If parts won’t tangle and surface damage won’t occur from contact between parts, then parts can be packed closely together and shipped in direct contact with each other. Parts that are uniform in shape, like some uniformly shaped metal sheets, can be packed without wasting any space.
Extra steps are necessary when parts shouldn’t be in contact during shipment to prevent deformation, scratching or other damage. Spacers or padding made from materials like foam, paper or wood can be used to prevent scratching and damage to the finish. Parts that nest together may only require paper between them, while other parts may need cardboard or plastic to separate them.
Where parts have sharp edges, extra protection may also be required.
Knocked-Down Sheet Metal Assemblies
If a sheet metal assembly is ‘knocked-down’, this just means that the different sub-assemblies and parts are separated for shipment and then re-assembled at the destination they’re delivered to.
This is a common option for automotive, rail, electronics and furniture, and it’s sometimes used as part of an import tax optimization strategy (think of the many “assembled in” incentives for products made in Europe or US from parts sourced elsewhere).
It’s often very economical to knock-down sheet metal assemblies because they tend to be bulky when fully assembled. When sub-assemblies, individual parts and components are separated, they can usually be packed much closer together.
Assembled Sheet Metal Part Packaging
Sheet metal assemblies can also be sent fully assembled. This is when no parts are separated out from a complete assembly during delivery. This is usually the least economical shipping method as it will take up the most space, but there are certain advantages as mentioned in the table above.
Where fully assembled products are sent directly to an end-user, packaging may need to meet branding requirements and destination labelling requirements. It may also need to include instructions or other printed inserts for the end user. As well as this, it will also need to fully protect the product during transport.
Custom containers are often the only option for certain complete assemblies because of their weight or dimensions. Larger products might need wooden crates, special pallets or other considerations.
Distribution Methods
Another factor which needs to be considered related to shipping method, is the distribution method for your product. Fabricators can package and ship your delivery directly to the end-user or to the next stage in your logistics cycle, such as to a distribution warehouse. Where your delivery is received has a big influence on how packaging should be designed.
Delivery to End User
Some fabricators offer drop-shipping services and will send parts or assembled products directly to customers. Alternatively, it will be sent to a distributor and then on to the end user. The condition of a product and the packaging it’s sent in reflects on your company. Packaging is a big deal when it’s part of a company’s branding. If you’re sending products directly to end users, then you need to provide packaging that protects the product as well as presents it in the right way. This could include custom branding on the box, instruction manuals, custom labels or special internal packaging to improve product presentation.
Delivery to Assembler
If a delivery is shipped to a location where parts or sub-assemblies will be assembled or integrated into another product, packaging doesn’t need to be so well presented. It does, however, need to be able to cope with all the steps it will take in the logistics cycle. The most important thing is that the part is protected by the packaging during transportation and storage.
Reusable packaging isn’t an option if the part is shipped to the end-user but is a possibility for regular shipments to distribution centers. This could mean plastic crates, pallets or other options.
Direct to Consumer
Direct to consumer, or D2C packaging, is a variation of Delivery to End User. This is generally for companies doing online sales, where the part is shipped directly via express company to the end user, and doesn’t pass through multiple warehouses or distribution points, isn’t pallet loaded and is shipped one by one. Because the unit is shipped singly, it means it can be subject to all kinds of abuse during the delivery method, and that it will need to be hand carried or at best, handled on a simple dolly to avoid additional shipping charges. In this case, a rule of thumb is that the carton should be less than 45 lbs, and protection needs to be of a higher level than other distribution methods.
Something also important for the designer to check is specific rules or regulations, size and weight limits published by the express delivery services (UPS, DHL, Fed Ex and others will have slightly different rules for different regions, so this should be checked with your delivery provider). This can help to avoid unexpected and often high surcharges for packages which get bumped into a higher weight / size class or require pallet delivery or lift gate trucks.
Calculate Preliminary Logistic Costs
Once you’ve determined the best *shipping option* for your product, it’s important to review the estimated cost to ship your part to determine if you’ve actually selected the right shipping and distribution methods.
There are several things to consider when evaluating potential logistics costs. The primary costs are going to be the cost to transport from the factory to warehousing or distribution, and then the cost to transport on to the final customer. Of course, any import taxes when shipping international will also need to be considered.
SHIPPING NEEDS | WHAT TO CONSIDER |
---|---|
Factory to Distribution Warehouse (3PL) |
|
Distribution Center (3PL) to End User |
|
Distribution Center to Shop / Dealer / Retailer |
|
Designing and Engineering Sheet Metal Product Packaging
After you’ve decided what the best shipping and distribution method for your product is, you can move onto the packaging design and engineering phase.
Packaging Engineering
Here are five steps you should follow in the packaging engineering process:
STEPS WHEN ENGINEERING PACKAGING | ||
---|---|---|
Step #1 Determine what packaging type to use. |
There are 2 packaging types you should consider: Type 1: The product supports the packaging. In this case, strength is less important. The main purpose of the packaging is to protect the product surface during shipping. Type 2: The packaging supports itself. In this case, the packaging must be strong enough to withstand shipping conditions. It also exists to protect the product and facilitate transportation. |
|
Step #2 Ensure geometry is continuous and that the product cannot move inside packaging. |
Type 1 Packaging: The product must also be strong enough to support other cartons so it can be palletized. Type 2 Packaging: The carton or insert must also be strong enough to support multiple cartons when products are palletized. Skip ahead to see different methods of protecting products that are inside a carton. |
|
Step #3 Check loadability inside truck or container. |
- With most products, it's best to design packaging so it is easy to load and unload by forklift. - Determine how you'll palletize the products and how it will be loaded inside the container or truck. - Keep in mind that the container door height is lower than the container internal height. |
|
Step #4 Validate expected logistics cost. |
Once you finish designing the packaging, you should confirm 3 things prior to producing packaging samples: - Validate container loadability. - Validate logistic cost. - Validate packing cost. |
|
Step #5 Drop test validation. |
- Test your packaging with samples. - Work with your freight forwarder or carrier to drop test your packaging. This will help to ensure your product won’t be damaged in the logistics cycle. - Your ultimate goal should be for the recipient to receive the carton in perfect condition. |
Packaging Carton Options
There are a lot of decisions to make around choosing a carton for your product. Most importantly, it needs to protect your goods during shipping. However, your choice also has an impact on your shipping costs and the way you will brand yourself. So some thought needs to be put in to balancing cost, size, branding, protection and other factors to select the optimal choice for your product.
Carton Choices
Most often, cartons come as boxes. These are available as either brown, white or custom printed, each with its distinct advantages and disadvantages.
Brown Boxes
- 60-100% recycled cardboard.
- Less expensive than white or printed.
- Easily available in a wide variety of standard sizes and strengths.
White Boxes
- Preferred for branding by some and allows for more printing options.
- Shows dirt and damage more than brown boxes.
- Can also contain recycled material.
- Custom printed boxes.
Colored Cartons
- Most costly option.
- Can be customized inside and out to support your brand.
- Can include instructions for the product.
- Requires additional lead time and minimum quantities may be required.
- Artwork and setup charges for each size of box and for any changes will be required.
Carton Strength
Your fabricator should help you find a box that offers the structure needed to ship your product. Factors that need to be taken into account are the dimensions of the box relative to the weight of the contents. It’s also important to consider the strength requirements during shipping and when cartons are palletized.
Boxes are made of corrugated paper which uses s-shaped paper flutes between linerboard paper to create its strength and structure. The thickness and number of flutes per foot impacts the strength of the box.
- A flute is 1/4” thick with 33 flutes per linear foot - provides the best cushioning properties.
- B flute is 1/8” thick with 42-50 flutes per foot - can resist crushing and has good stacking strength.
- C flute is 3/16” thick with 39-43 flutes per foot - common choice for shipping.
Double and triple wall corrugated containers offer better strength and protection than single wall.
Carton Testing
The packaging industry uses Mullen burst tests and edge crush tests to guide strength levels for boxes.
- The Mullen burst test standard is often used by those who are concerned about damage during handling throughout the logistics chain.
- The edge crush test helps understand how a box will hold up when stacked or palletized.
To understand how to interpret these standards, an edge crush test of 26 ECT means a carton can withstand 26 pounds of pressure on its edge.
A Mullen burst test score of 150 means a carton can withstand 150 pounds per square inch of force applied to its face.
Single Wall Corrugated Box Strength Guide According to Content Weight
MAXIMUM LOAD PER BOX | MINIMUM EDGE CRUSH TEST | MULLEN BURST TEST |
---|---|---|
35 lbs | 26 ECT | 150# |
50 lbs | 29 ECT | 175# |
65 lbs | 32 ECT | 200# |
95 lbs | 44 ECT | 275# |
120 lbs | 55 ECT | 350# |
Internal Packaging Materials
If there is space between a product and the carton in which it’s packaged, it’s often necessary to add internal packaging. This provides padding for the product and also prevents it from moving inside the carton.
EPE (Expanded Polyethylene) Foam
EPE foam (expanded polyethylene foam) has a low density and is semi-rigid with closed cells.
It’s commonly used for cushioning and impact absorption.
Advantages
- No odor or taste. Food safe
- Lightweight with a high weight to strength ratio
- Very flexible
- Good shock absorption, cushioning and insulation
- Resistant to water, oil, static and some chemicals
- Recyclable and reusable
- Doesn’t degrade or break down as easily as EPS – much cleaner presentation for end customer
Disadvantages
- More fragile than traditional foam
- Deforms much more easily than EPS
- Recycling facilities may be limited for end user
Customized EPS (Expanded Polystyrene) Foam
EPS foam (expanded polystyrene) is a white, rigid foam that can be custom formed to suit the needs of a part or assembled product. It’s produced from small, solid polystyrene beads and has a closed cell structure.
Advantages
- Can be formed or molded into a custom shape to protect a part
- Offers a tight fit for sensitive items
- Custom shapes to contain part or molded corners are possible
- Lightweight and stackable
- Very good impact strength and shock absorption
- Low moisture absorption, chemically inert, bacteria resistant and food safe
- Good insulation and cushioning properties
- Does not contain CFCs or HCFCs and is recyclable
Disadvantages
- Requires lead time for customization
- Additional costs for developing custom design and tooling to ensure good part cushioning
- Any changes to product or packaging will require changes to EPS mold which will impact budget and timing
- Jig cut EPS (without a mold) is costly and slow
- Material is brittle and can break into pieces. It can also shed particles when rubbed
- Flammable and can degrade when exposed to UV light
- Recycling facilities limited for end users
- Not biodegradable
- Certain markets and retailers restrict its use in packaging (EU, major retailers like Walmart, Ikea, etc.)
Internal Cardboard Dividers
Internal cardboard dividers provide a place for individual parts within a carton. This prevents parts from moving within a carton and coming into contact with other parts. It also keeps them still during transit.
Advantages
- Saves the expense of using separate cartons for individual parts
- Highly economical
- Custom sizes are available
- Recyclable and doesn’t contain CFCs or HFCs
- Highly suitable for small and delicate items
Disadvantages
- All products within a carton must be a uniform size
- Often, only certain sizes are available
- Lead time is required for customization
- Flammable and not water resistant
- Recycling facilities may be limited for end user
Molded Paper Pulp
Typically made of recycled paper, molded paper packaging is available in different thicknesses and can be molded to fit a specific part.
Advantages
- Can be formed or molded into a custom shape to protect a part offering a tight fit for sensitive items
- Custom shapes to contain part or molded corners are possible
- Very strong with good shock absorption and cushioning
- Less expensive than many other foam and plastic packaging
- Water resistant, electrically neutral and resistant to temperature changes
- Made from recycled materials, and is recyclable, biodegradable and compostable
Disadvantages
- Requires lead time and additional costs for customization and mold design
- Changes to product or packaging will require changes to mold and impact budget and timing
- May be heavier than other options, increasing shipping costs
- Treatment required to make it completely waterproof and not just water resistant
Plastic Bubble Wrap
Plastic bubble wrap is made from rows of cells with air between layers of polyethylene. Bubble sizes can vary based on the needs of the product, including larger “air pillows” to fill large voids.
Advantages
- Used to wrap parts or fill voids
- Flexible and suitable for a wide variety of products
- Good shock, vibration and surface protection
- Inexpensive, lightweight and anti-static
- Some are more environmentally friendly with pre and post-consumer waste incorporated
- Reusable
Disadvantages
- Air seals can be punctured compromising the cushioning ability
- Recycling facilities may be limited for end user
- Not biodegradable
Paper Void Fill
Packing paper, like bubble wrap, can be used to fill voids. It’s typically used on the top and bottom of boxes to provide cushioning to the product inside.
Advantages
- Good cushioning and surface protection
- Inexpensive
- Recyclable
- Can be branded if required
Disadvantages
- Compresses so a lot of material is required to provide appropriate cushioning
- Adds weight to package
- Doesn’t protect against moisture, chemicals, oils, etc.
Corrosion Protection During Shipping
Proper packaging can help prevent corrosion, should your sheet metal fabricated parts be exposed to any corrosive elements.
Appropriate packaging is a good investment for parts or assemblies that are sensitive to corrosion and will be transported in conditions that expose them to moisture, chemicals, or significant changes in temperature or humidity.
There are several options:
Bags and Desiccants
Bags can be used to act as a barrier to stop parts being exposed to moisture. The material used to create a bag will depend on the parts in question and the exposure levels a shipment will undergo. Bags can also be antistatic to protect from electrostatic discharge.
Silica gel or activated clay are common choices for desiccants to control humidity levels.
For large containers, desiccant strips are often hung inside.
Foil Vapor Barriers
Parts that are prone to surface damage can be packaged using a water vapor proof foil barrier that is vacuum sealed.
Prior to being placed into the foil package, material is often used to cushion the part, and a desiccant is enclosed. It’s also possible to include a humidity indicator card inside a component of the packaging that can be opened and checked for humidity levels periodically during shipment without exposing the part itself.
This form of packaging is a best practice for parts that require very low humidity during shipment and is often used for ocean transport.
Material Type | Advantages | Disadvantages |
---|---|---|
EPE Foam | No odor, lightweight, flexible, good shock absorption, water-resistant | More fragile, deforms easily, limited recycling for end-user |
Customized EPS Foam | Can be molded, lightweight, good impact strength, recyclable | Customization lead time, brittle, flammable, restricted by some retailers |
Cardboard Dividers | Economical, recyclable, suitable for small items | Uniform size required, flammable, not water-resistant |
Molded Paper Pulp | Strong, shock absorption, water resistant, biodegradable | Customization lead time and costs, heavier |
Plastic Bubble Wrap | Flexible, good protection, lightweight, inexpensive | Can be punctured, not biodegradable |
Paper Void Fill | Good cushioning, recyclable, can be branded | Compresses easily, adds weight, not moisture-resistant |
Bags and Desiccants | Moisture barrier, can be antistatic | Depends on material for effectiveness |
Foil Vapor Barriers | Water vapor proof, ideal for low humidity, best for ocean transport | Requires careful packing with desiccants and cushioning material |
Package and Product Labeling for Sheet Metal Parts
How you label your product will vary based on several factors, including the type of product and the geographical markets you’re shipping into.
Sheet Metal Part Labeling Options
Sheet metal can be marked or labeled through different methods, including electrochemical marking, lasers, or screen printing. This is done to identify part numbers or add branding or other identifying information.
Your labeling and packaging should support your brand and can be included on boxes, on-product labeling and possibly on other shipping materials.
Knocked-down assembly kits should be labeled for easy handling and assembly at their destination.
When multiple products are boxed and shipped together for additional distribution, the external boxes should be labeled to support logistics and inventory management at warehouses.
Different local markets have different requirements for labeling standards so confirm what’s required and work with the help of your fabricator or an advisor.
- Some products require permanent markings on the product themselves including products for small children.
- Labels shall include traceability # to track design change and enable inventory control according to good practices.
Komaspec Sheet Metal Fabrication
Our team of engineers and technicians here at Komaspec have more than 20-years’ experience in sheet metal fabrication and assembly of sheet metal products. We’re happy to help review your product design together and select the fabrication processes that best suits your product’s needs, whether it’s laser cutting, bending, stamping, etc..
As part of our turnkey manufacturing services, we also put our extensive experience to use helping with packaging design Whether it’s custom designed cartons, integrated pallets, molded foam packaging or special wooden crates, we’ll find the right packaging for delivering your product safe and sound.