Vertical Integration in Sheet Metal Manufacturing
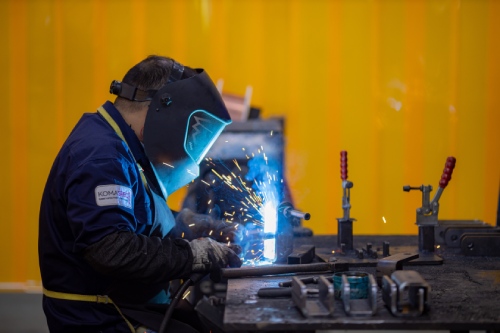
Introduction
When looking for a sheet metal fabricator for your products, their level of vertical integration becomes a key selection criterion. In sheet metal fabrication, as in many other sectors, vertical integration in manufacturing has a direct bearing on your costs, product quality and the turnaround time. In this guide—on vertical integration in sheet metal fabrication--we explore what factors are in play and why the level of vertical integration matters in your selection of sheet metal fabricators.
This guide covers:
- What is vertical integration?
- A deep dive into vertical integration
- Why backward vertical integration is important in contract manufacturing
- How vertical integration drives innovation in sheet metal fabrication
What Is Vertical Integration?
Vertical integration is a business strategy in which a company streamlines its operations by gaining direct ownership and control of more than one stage of the supply chain. It has the goal of gaining and expanding control over one's supply chain (“Vertical Integration”).
The vertical integration could be a move forward, towards their end consumer or a move backward towards securing raw materials and assembly works for production. Diagram 1 shows the choices available to a business for vertical integration.
Diagram 1: Vertical integration in manufacturing
Forward Integration
Forward integration is the strategy in which a company, say in contract manufacturing, opts to buy or merge with distribution and marketing operations, enabling it to offer better prices and service to its customers. With forward integration, the combined business gains better control over the business activities that lie ahead in the business value chain (Corporate Finance Institute, “Forward Integration”).
Diagram 2: Forward Integration
Backward Integration
Backward integration is a business strategy in which a company--say in manufacturing--buying its supplier, subcontractor, or an assembly plant instead of relying on outside third parties and contractors. With backward integration, the acquiring company gains control over business activities that lie behind in their business value chain (Corporate Finance Institute, “Backward Integration”).
Diagram 3: Backward integration
Henry Ford was a big believer in vertical integration. He did not stop at vertically integrating the sheet metal parts of Ford cars. He went so far as to buy South American rubber plantations so that he could ensure the continuous supply of rubber for the tires of the Model T's! The main purpose of backward integration is to get the benefit of economies of scale. However, beyond costs, there are infinite benefits that accrue contract manufacturers pursing backward vertical integration.
Why Backward Vertical Integration Is Important in Sheet Metal Contract Manufacturing
First a look at the metal fabrication industry
Metal fabrication is the process of making machines and structures using raw metal materials. Metal fabrication process includes cutting, burning, welding, machining, forming and assembly of parts to create the end product. From handrails to heavy equipment and machinery, from nuts and bolts to car bodies and vehicle parts, metal fabrication industry has broad applications. It is a key contributor to the aerospace, construction, automotive, agriculture, mining and consumer goods industries as well as to the electronics and energy sectors.
Sheet metal fabricators produce a wide range of components using a wide variety of materials including sheet metal, fittings, castings, formed and expanded metal, flat metal, sectional metal and welding wire. These call for a corresponding range of specialized equipment for pipe and tube processing, plastic injection, laser cutting, threading and chamfering, surface finishing, stamping and welding to produce all these parts (“Sheet Metal Manufacturing Process and Its Operation Types | Engineering”). Not all sheet metal fabricators have the ability to invest in all of this equipment, which means resorting to subcontracting a substantial part of the work. However integrated the supplier, there may still be some processes outsourced - however, generally the goal is for these to be non-core processes, which require minimal skill or expertise, or they may be processes that can be controlled relatively easily.
Why Contract Manufacturers and Sheet Metal Fabricators Seek to Vertically Integrate Their Operations
Companies in sheet metal manufacturing decide on a backward vertical integration strategy for several reasons:
- To reduce their costs of production
- To strengthen their supply chains and assure continuity of supply
- To reduce lead times
- To improve control of quality and source
With backward integration, the acquiring company gains control over business activities that lie behind in their business value chain. By buying a supplier or bringing a hither to external production process in-house reduces the reliance on third parties and contractors. The contract manufacturer gets the benefit of economies of scale and can bring down manufacturing costs. At the same time, the increased level of control over supply chain and manufacturing processes also contributes to better lead times and quality of output.
Advantages of Vertical Integration in Sheet Metal Manufacturing
Sheet metal fabrication companies seek backward vertical integration by acquiring expertise and processes that were as previously outside of the business in view of the many benefits.
Better cost control and economies of scale
Owning the core manufacturing processes and technologies helps get a better handle on product costs. The sheet metal fabricator that seeks backward vertical integration--if they manage the integration process efficiently and effectively--will get the benefit of greater efficiencies and productivity and reduction in costs.
Fig. 1 Manual welding at Komaspec
Cost reduction does not come solely from better efficiencies. It also comes because the company then effectively cuts out excessive supplier margins that get accumulated up the supply chain. Vertical integration can also help drive down waste and procurement costs. Companies within the same group can work on becoming more competitive at the end level.
Having a greater control over the quality of raw materials and parts supply will also help bring down cost of production directly because of the elimination of middleman margins. Indirectly, it offers better control over inventory management and working capital costs (“Is Vertical Integration Profitable?”).
All of this translates to the sheet metal manufacturer being able to offer better rates to their customers thus enhancing their price competitiveness. This is really a key driver for backward vertical integration in sheet metal manufacturing industry.
Better control over delivery times
When core processes are performed inhouse, the sheet metal fabricators can exercise better control over the key aspects of production and procurement, reducing the uncertainties and potential delays associated with outside contractors. This means they are able to offer definite lead times without building in a time-margin for events and delivery factors outside their control. For a client, this is another key advantage of working with a vertically integrated manufacturing company.
Better control over quality of output
Backward integration means a better control over the supply chain and a better handle over the quality of material coming up the supply chain. If you are buying goods from a subsidiary, you do not need to waste time and effort looking for the best suppliers. They can simply focus on production or sourcing, without worrying about procurement aspect.
Disadvantages of Vertical Integration
The biggest disadvantage for vertical integration in the sheet metal industry is the steep initial cost. Capital expenditure for acquiring modern, networked or automated equipment can be substantial. And there will need to be significant investment in management time, skilled labor and effort in order to bring more and more of the production process under the same roof.
Other disadvantages include straying from the core. Companies may end up less organized and less strategically aligned if their integration efforts are not carefully contemplated and effected. There may be problems of integration which result in losses of time, effort and escalating costs, where the integration is not properly managed.
Despite the large initial outlay, sheet metal fabricators pursue vertical integration because the benefit of a strategic advantage in providing a superior service to their customers with greater control over quality and costs.
How the Clients Gain From Using a Vertically Integrated Metal Fabricator
When it comes to sheet metal fabricators, it is the backward integration that should be of concern to clients, because that is what leads to better cost controls, continuity of supply chains, reduced lead times and quality assurance in the output.
Such sheet metal fabricator can perform the work of many vendors and subcontractors under one roof. They can work on parts in parallel without having to queue behind other customers to get their parts produced by a sub-supplier. This helps cut down your delivery times. On the other hand, it also cuts down on your product cost, because it is not loaded with vendor margin on top of vendor margin. Apart from that, a vertically integrated sheet metal fabricator can naturally offer you the benefit of their economies of scale.
They have the expertise inhouse to guarantee the quality at every stage. This evidently converts to less rework and factory waste. It delivers you production efficiencies without the headaches.
Fig. 2: Sheet metal fabrication and welding area at Komaspec
For you, this means you can get your product made without too much stress and excessive cost overruns. You do not have to push and pull your product through layers and layers of contractors, each with their own issues on quality, cost, delivery times and the documentation. With a vertically integrated contract manufacturer you just work with one party who will handle all of your needs and deliver you the product of a quality and in volumes that you specified.
Part design, design for manufacturing and design for cost savings all benefit from vertical integration as well. By leveraging their deep knowledge of what drives costs, lead times and creates quality issues in various production processes like laser cutting and CNC bending, vertically integrated sheet metal manufacturers are the best resources for optimizing part design and cost, a benefit that comes at no increased cost to their customers and will often, in fact, save them money.
How Vertical Integration Drives Innovation in Sheet Metal Fabrication
The global sheet metal fabrication services market was estimated to be worth USD 15.81 Billion in 2020 and is expected to have reached USD 16.31 Billion in 2021. By 2026, with a Compound Annual Growth Rate (CAGR) of 3.46%, it is expected to reach USD 19.40 Billion (“Sheet Metal Fabrication Services Market Research”).
Strategic Trends in Sheet Metal Fabrication Services
In recognizing the immense growth potential, the global industry offers, the sheet metal fabrication contract manufacturers who opt for vertical backward integration, are investing in the advanced equipment, technologies and processes that are necessary to truly benefit from the scale that integration offers. The bigger the scale the more sense it makes to invest more in advanced technologies. The increasing demand from major end-user industries and the rising demand for sheet metal fabrication services from construction has underwritten this move towards more integration and more investing in advanced manufacturing.
There is an increasing focus on lean manufacturing and achieving greater operational efficiencies. While some fabricators struggle with technology modernization, the more persistent have managed to move forward leaving their peers behind.
Investing in Sophisticated Manufacturing Systems
Most vertically integrated manufacturers have invested substantially in advanced technologies, machinery and equipment, including automation. They have professionally trained staff and inhouse expertise to oversee the operation of these systems. Their state-of-the-art automated manufacturing systems offer greater scale, more complex quality systems and capabilities compared to what smaller, tier 2 or 3 sub-suppliers can offer.
Fig 3. LVD Fiber Laser Cutting Machine at Komaspec
Here are some of the top trends that have helped bring the sheet metal industry closer to industry 4.0:
Automation
To some sheet metal fabricators automation is still on the way. But to others, that powerful future is already here. Robotic technologies have simplified the act of cutting and bending sheet metal. Automation also helps manufacturers achieve precision in their operations and minimize material waste.
Additive fabrication or 3-D printing
3-D printing is no longer the future in sheet metal fabrication. Many metal fabrication businesses worldwide are enjoying the benefits of 3-D technology that is already an integral part of their manufacturing operations. These benefits include time and cost reduction through elimination of some assembly steps, gaining greater design freedom and minimizing material waste. All of these ultimately helping improve production quality.
Tube laser technology
Tube laser technology, one of the fastest growth sheet metal fabrication technologies, offers many advantages over the traditional processes. The tube laser machines possess the capability to make sharp, intricate cuts, thus helping improve both fabrication quality and speed. This too reduces material waste and cuts down assembly costs.
ERP systems
Adoption of enterprise resource planning (ERP) systems enable them manage accounting, procurement and supply chain operations as well as risk and project management smoothly (“What Is ERP?”).
Investments in these and other technologies enable the contract manufacturers undertake design and manufacturing that can now happen under the same roof. Potential for immediate feedback and faster improvement deliver cost, quality and timeline benefits.
A better understanding of the factors critical for quality output allows for smart investment. Automation together with investments in precision manufacturing equipment contributes to enhance quality of output. Automation means higher quality, more granular data on manufacturing operations. This can in turn lead to better design and improved use of research and development (R&D) budgets.
As a result of investing in the latest technologies today's vertically integrated sheet metal fabrication companies run sophisticated operations.
- They operate smart factories with high levels of automation
- They work with their clients and design houses to design for manufacturability and assembly (DFM).
- They run lean manufacturing operations that make them cost competitive
- Have sophisticated quality performance tracking for their manufacturing processes.
- Can work on reverse engineering projects and offer customized solutions
- They can reproduce items using state-of-the-art drafting, designing and construction using 3D modelling and CAD-CAM technology (computer aided design and computer aided manufacturing)
All this and more enable them to compete in the hyper competitive field of contract manufacturing (in China).
Summary
In this guide we looked at vertical integration and took a deep dive to understand why backward integration in sheet metal fabrication makes sense for contract manufacturers.
To summarize, here’s why a vertically integrated sheet metal fabricator is infinitely preferable to one that is not:
- Smart factories. Investments in advanced technologies, machinery and equipment, together with professionally trained staff and inhouse expertise to oversee the operation of these systems.
- Costs can be kept under control more effectively. Sophisticated systems translate to enhanced systems of management and control. These helps identify and troubleshoot operations, help avoid cost over runs and minimize machine downtime.
- Quality can be better assured. The manufacturer directly oversees processing on-site with quality and production engineers ready to step in in case of issues. They can spot problems earlier.
- Lead times become shorter. and turnaround is quicker because most functions are performed in-house or with subsidiaries and automated to a significant degree.
With their state-of-the-art automated manufacturing systems, precision manufacturing capabilities and quality control systems are able to offer competitive pricing and superior service for clients seeking contract manufacturers in sheet metal fabrication. Smaller, lesser integrated second or third tier sub contactors are no match for these companies.
Here at Komaspec, our more than 15 years of experience in sheet metal fabrication and contract manufacturing in China mean that we are a leading choice for companies looking for China-based Contract Manufacturers. With exceptional in-house integration, NPI and DFM experience, and thousands of successful manufacturing projects, we provide service to a range of customers and industries.
To learn more about our Contract Manufacturing services here at Komaspec, please follow the link below, or to quote a project, please click through the “Request a Quote” button below.
FAQs
What are the types of vertical integration?
Vertical integration can happen in two directions:
- Forward vertical integration is when a company integrates with one of their buyers, distributors or retailers. The company undertaking forward vertical integration is basically solidifying their market position and getting one more step closer to their ultimate market, whether business or consumer.
- Backward integration is when a company integrates with another who is part of their supply chain. Backward integration is a strategy that helps bring material suppliers, parts manufacturers, subcontractors giving the integrating company better control over material and parts costs, quality and delivery times. In turn, backward integration enables the company realize economies of scale and solidify their competitive pricing.
What do you mean by vertical integration? Give two examples.
- A company in fast moving consumer goods (FMCG) may buy or start a distribution company and get the better control over their distribution processes.
- A distribution company may merge with a retailor to get a stronger hold of the market.
What is vertical vs horizontal integration?
Horizontal integration is a business strategy where a business grows by acquiring other companies in their industry operating at the same point in the supply chain. Vertical integration is when a business expands by acquiring another company that operates before or after them in the supply chain. The vertical integration could be a move forward, towards their end consumer or a move backward towards securing raw materials and assembly.
What is vertical integration in manufacturing?
A manufacturer can seek to integrate vertically by acquiring or merging with companies in two directions, either going forward in the supply chain or reaching back. If a manufacturer integrates with a parts manufacturer, one of its subcontractors or with a supplier of materials, that is considered vertical, backward integration. If a parts supplier integrates with a manufacturer getting one link closer to its customers in the process, that is considered forward vertical integration.
Do sheet metal fabricators give quotes online? Are they valid?
Some manufacturers with smart factories and advanced manufacturing systems are able to provide quotes for standard items online. They are able to do this because they have streamlined procurement and production systems and automated their manufacturing processes, enabling them calculate costs for producing a specific item in a given volume.
However, if you have a specialized, non-standard item which would require reverse engineering or design capabilities, this type of item may not be available via online quotations. For these, you may need to contact the manufacturer and discuss the product specifications.
What are smart factories when talking about sheet metal fabrication?
Smart factories are an opportunity to create new forms of efficiency and flexibility by connecting different processes, information streams and stakeholders (frontline workers, planners, etc.) in a streamlined fashion (“Definition of Smart Factory - Gartner Information Technology Glossary”). Smart factory initiatives might also be referred to as “digital factory” or “intelligent factory.”
A smart factory or intelligent factory is one that contains a series of smart machines that are governed by a single system. In a smart factory, automated sheet metal machines will work in succession to each other without requiring human intervention or with minimal intervention. The result is an efficient production process. Smart factories enable the production of unique and complex designs as required by clients, which traditional factories would find challenging.
Smart manufacturing is the result of combining internet software that helps in the monitoring of production machinery. Use of intelligent systems minimizes the chance of errors that may be present in the item produced. Smart factories do not require the manufacturer to inspect all products in a uniform sequence. Smart factories offer a viable solution where mass production is desired, especially in in sheet metal fabrication.
Will a sheet metal fabricator work with my design house?
That depends on the sheet metal fabricator and their capabilities. Some sheet metal fabricators only produce standard parts and are not open to working with clients in design for manufacturing or design for assembly projects. Others who have the design for manufacture capabilities and the bandwidth will work with clients and their design houses on product designs before undertaking the manufacturing of the designed items.
What is lean manufacturing?
Lean manufacturing is a manufacturing methodology that focuses on minimizing waste within systems while also maximizing productivity at the same time using principles such as continuous improvement (Landau). In lean manufacturing waste is any manufacturing process that does not add value for a customer which a customer would not be willing to pay for.
The seven types of waste identified and eliminated by lean manufacturing include:
- Costs of unnecessary transportation
- Excess inventory
- Unnecessary movement of people, equipment or machinery
- People waiting or idle equipment
- Over-production of an item
- Manufacturing defects that require rework and extra costs for corrections
- Over-processing. This means putting in more time than necessary from what a customer needs, such as using high tech machines of trivial product features.
Works Cited
- Corporate Finance Institute. “Forward Integration.” Corporate Finance Institute, 30 June 2020, www.corporatefinanceinstitute.com/resources/knowledge/strategy/forward-integration.
- “Vertical Integration | Definition, Example, and Facts.” Encyclopedia Britannica, www.britannica.com/topic/vertical-integration. Accessed 28 Dec. 2021
- Corporate Finance Institute. “Backward Integration.” Corporate Finance Institute, 29 June 2020, www.corporatefinanceinstitute.com/resources/knowledge/strategy/backward-integration.
- “Sheet Metal Manufacturing Process and Its Operation Types | Engineering.” Engineering Notes India, 23 July 2018, www.engineeringenotes.com/thermal-engineering/sheet-metal-working/sheet-metal-manufacturing-process-and-its-operation-types-engineering/49541.
- “Is Vertical Integration Profitable?” Harvard Business Review, 1 Aug. 2014, www.hbr.org/1983/01/is-vertical-integration-profitable.
- “Sheet Metal Fabrication Services Market Research.” Research and Markets Ltd 2021, www.researchandmarkets.com/reports/4985956/sheet-metal-fabrication-services-market-research. Accessed 28 Dec. 2021.
- “What Is ERP?” SAP Insights, 7 Dec. 2021, www.insights.sap.com/what-is-erp.
- “Definition of Smart Factory - Gartner Information Technology Glossary.” Gartner, www.gartner.com/en/information-technology/glossary/smart-factory. Accessed 28 Dec. 2021.
- Landau, Peter. “What Is Lean Manufacturing?” ProjectManager.Com, 15 Nov. 2021, www.projectmanager.com/blog/what-is-lean-manufacturing.