At Komaspec we pride ourselves as a world-class manufacturer that complies with i4.0 principles. The digital connection of all machines and technical devices through our tablet application makes all manufacturing processes visible and controllable in real-time. As a result, we are able to systematically manufacture complex assemblies.
Our Approach
Execute systematically complex assemblies from drawings to finish products, fast lead time, real-time visibility to all stakeholders and high efficiency enable us to provide a competitive edge to Brands and OEM worldwide.
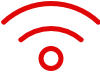
Smart Factory
Smart factories are the future of the manufacturing industry. Komaspec is devoted to driving this concept into reality, working towards the automation of production processes and logistics systems without manual interference. Our equipment and modern execution systems are the backbone of realizing this goal. Benefits of this move have been evident in such aspects as manufacturing efficiency, labor costs reduction and waste elimination.

Reverse Engineering
Komaspec is a solution-giving company and reverse engineering is an important part of it. We extract knowledge or design information from our manufacturing process and products and are able to reproduce the product based on the extracted information. We draft, design and reconstruct according to the specific needs of our customers in 3D models. Reverse engineering has helped us to better analyze control and improve the manufacturing process.

Quality Performance Tracking
Pivot88, the digitized quality control platform, facilitates the monitoring and inspection of all processes in real time, providing more visibility and transparency along the manufacturing process. Additionally, Komaspec provides our customers with individual access to the system, allowing them to monitor all the processes of their product parts’ development and finalization in real time.

Lean Manufacturing and 6S
Implementing lean manufacturing has allowed Komaspec to constantly hold low inventory to eliminate waste. Maintaining a close and trustful partnerships with our suppliers has also enable Komaspec to ensure a rapid and smooth flow of products and components into our facility.

Lead Time
Short lead time and quicker turnaround are vital for every process in Komaspec, both within and outside the factory. Our tablet system enables immediate updates and implementation of instructions throughout the construction phase, leading to time and cost optimization.

Design for Manufacturability
Design for manufacturability (DFM) is an engineering art of designing products to improve the ease of manufacturing. Through modeling of products and systems in a virtual environment, our top-notch engineering team is able to identify and resolve potential or existing structural and performance issues, thereby, reducing manufacturing costs and improve design for manufacturing efficiency.
Industry 4.0 takes manufacturing to a whole new level
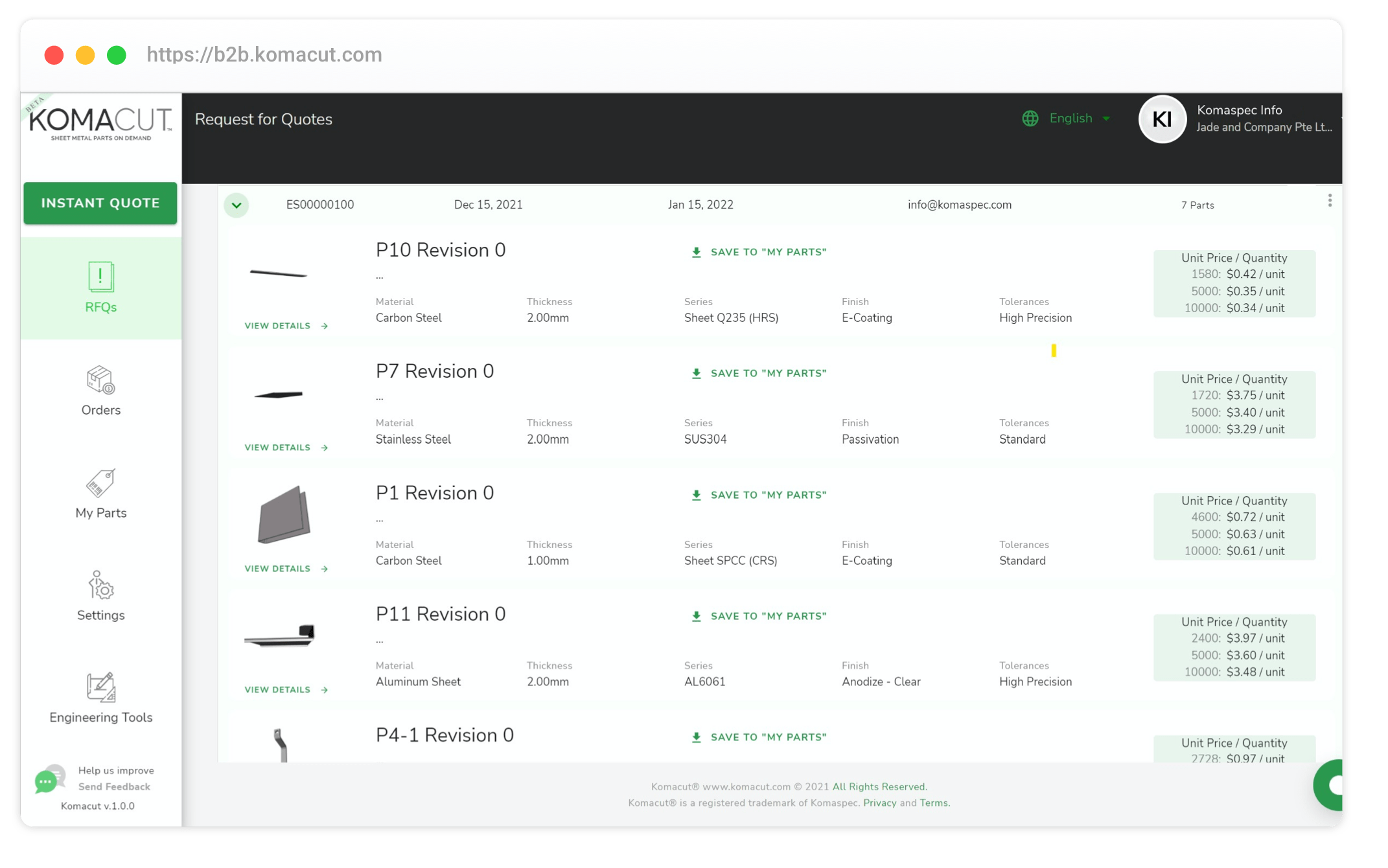
Provides all team members with extreme visibility to execute and enable decision-making, savings time and cost.
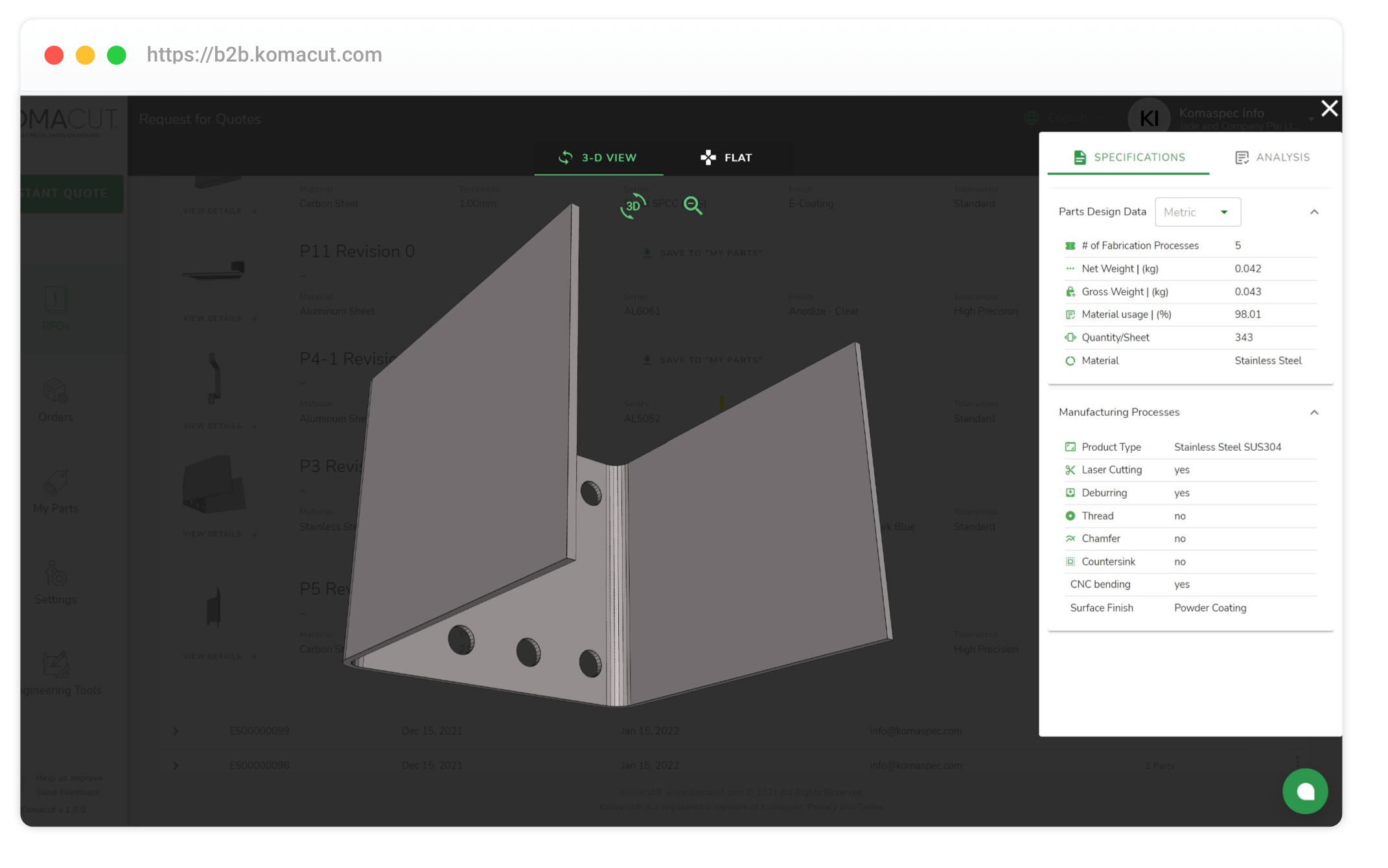
Utilizing industry 4.0, customer-specific manufacturing requirements can be executed within expectations, and manufacturing and maintenance processes can be considerably improved and automated.
In order for us to provide unmatched customer experiences and continue our innovation journey, our team must be supported by user friendly IT systems and latest technologies equipments.