How to Choose a Surface Finish for My Sheet Metal Product
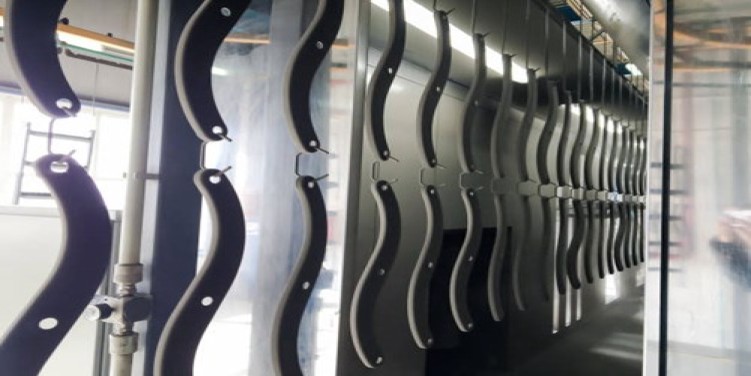
Different metal finish options
There are different metal finishing options for sheet metal fabrications.
Metal finishing involve adding a layer to the part surface like powder coating or plating.
In this article we discuss surfaces preparation and surface finishes which removes material from the part surface to improve the finishing performance and appearance post finishing.
Choosing the right surface preparation helps improve the performance and longevity of the part but you need to consider that not all finishes are suitable for all metal types.
Order and track sheet metal components online through Komaspec's on-demand sheet metal fabrication platform.
Sand blasting
Abrasive shots (sand, walnut shells, metal soda ash, or others) are forced at high speeds against the part to smooth and clean the surface.
Small and medium sized parts undergo sand blasting on an automation line typically, while larger parts use a sandblast chamber.
Advantages:
- Commonly used to prepare surface for additional finishing like powder coating or metal plating
- Smooths surface defects
- Cleans surface
- Improves corrosion resistance
Disadvantages:
- The shot medium should be chosen based on the metal of the part because heavy shots can damage soft metals
- Will not remove oils or similar contaminants
- Process can produce enough heat to warp metals like aluminum
- The material used to blast the parts may stick to the parts and create imperfection during finishing process like powder coating
Commonly used for:
- Stainless steel, carbon steel
- Parts requiring a uniform, matte texture
Metal grinding
There are different types of equipment that can be used to apply friction to the metal surface and create a smooth or decorative finish.
The degree of smoothness is determined by the material used to make the part and the type of grinding equipment used.
Advantages:
- Removes surface imperfections
- Can create a very smooth finish
- Good option to remove welding splatter and hard to remove burrs formed from other processes
Disadvantages:
- Often a manual process which can increase labor costs
- Manual process comes with risk of inconsistencies
Commonly used for:
- Parts with large welds or requiring significant edge treatments
Tumbling and Rumbling
Commonly used to smooth edges and remove burrs, tumbling involves adding the metal into a drum along with abrasive pellets where they are subjected to tumbling.
Rumbling is a similar process with the addition of vibration.
Advantages:
- Machine speed and vibration can be adjusted to accommodate different treatments
- Fast process able to accommodate large production runs
- Can accommodate different finish standards from basic burr removal to mirror finishes
- Consistent finish across parts
Disadvantages:
- Can damage parts if not done correctly
- Delicate or detailed parts generally shouldn’t be tumbled, however vibration is an option
Commonly used for:
- Both small and medium size parts
- Often used for large batches or small parts
- Parts made of hard metals
Automatic deburring and edge rounding machine
Commonly used to smooth edges and remove burrs for flat pattern sheet metal parts of all size, immediately after laser cutting process.
Advantages:
- Consistent burr removal
- Fast process able to accommodate large production runs
- Can accommodate different finish standards
- Consistent finish across parts
- Improve paint adhesion at powder coating process on steel parts
- Removes rust
- Some auto deburring machine also have surface finishing module to create brushed linear finish on aluminium and stainless parts
Disadvantages:
- Can damage parts if not done correctly
- Limited for parts with material thickness from 1.0mm to 20.0mm
- Parts size limitation will depend on the size of the auto deburring machine
- If the parts are too small(less than 20mm diameter), auto deburring machine can’t be use
- Does not remove laser cut oxidation on the laser cut parts edge
Commonly used for:
- Both small, medium and large size parts
- Often used for large batches
- Parts processed from laser cutting or CNC punching with flat pattern. Auto deburring and edge rounding can only be use for parts that are flat (prior to CNC bending)
Metal polishing
A cloth wheel or polishing machine is used to buff the surface to a smooth finish.
Generally, a series of progressive wheels or belts to get the desired finish.
Advantages:
- Highly decorative, smooth, glossy finish
- Sometimes used to prepare surface for plating
- Removes oxidation
- Removes scratches or minor surface imperfections
Disadvantages:
- Process creates rounded edges
- Not well suited to parts with detailed or fragile features
- Doesn’t improve paint adhesion so not used for parts to be painted
- Labor intensive
- Challenging for parts with inconsistent shape and/or hard to reach areas
Commonly used for:
- Parts requiring a smooth finish and glossy sheen
- Decorative parts
- Stainless steel, copper, or aluminum sheet metal
We are glad to review your product design together and help you select the fabrication process that best suits your product’s needs.