- CO2 Lasers
- Fiber Lasers
- Fiber vs. CO2 Lasers
- Choosing Laser Types
- Materials Suitable for Laser Cutting
- Materials Unsuitable for Laser Cutting
- Laser Cutting Advantages
- Laser Cutting Disadvantages
- Applications of Laser Cutting
- Usage of Laser-Cut Parts
An Engineer's Guide to Laser Cutting
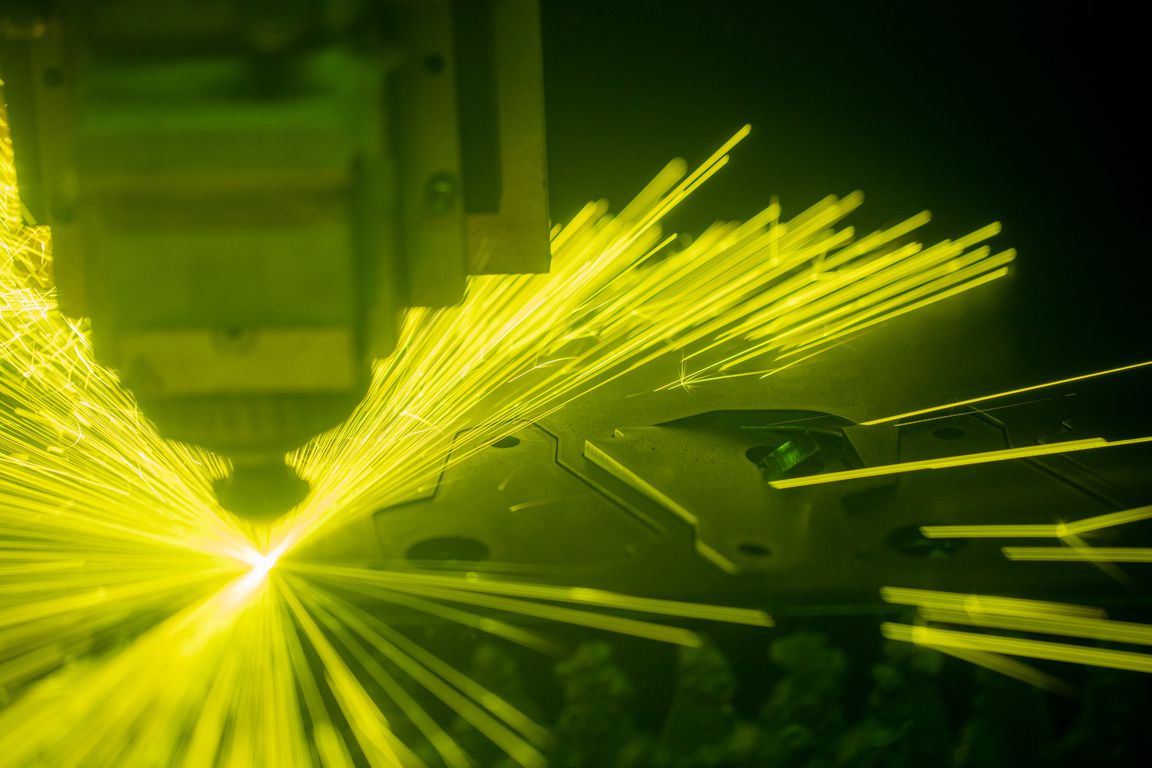
Table of Contents
Introduction to Laser Cutting
The term LASER is an acronym for “light amplification by stimulated emission of radiation.”
When a laser is used, light is intensely focused onto an object at a particular point. This focused light (referred to as ‘spatially coherent’ light) causes an extreme elevation in the temperature of the illuminated area. The material under the illuminated area melts rapidly or is vaporized, and a cut or fissure forms in the material.
Fig.1: Laser Cut Parts
The basic idea behind laser cutting is simple. Carrying out laser cutting in practice, however, relies heavily on the use of advanced equipment, technology and expertise in cutting methods. To get the best results at a manufacturing level, a good deal of expertise and care are needed when methods and technologies are chosen.
In this guide, we’ll explain what the most common modern laser technologies and processes are, where they’re best applied and how laser cutting compares to other cutting technologies.
A wide variety of materials can be formed or processed through laser cutting. The most frequently laser cut materials are common metals like mild steels, stainless steels, steel alloys and aluminum. A wide range of other metals can also be cut. As well as metals, other materials, like wood, plastics and ceramics, can all be cut with lasers.
Laser cutting technology has evolved considerably within the last twenty years or so. Nowadays, the engineer has a very wide choice of lasers, machining principles and computerized controls. Lasers can now be used to cut materials to a level of accuracy that wasn’t possible in the not-too-distant past.
Stimulated Gas Emission Lasers (CO2 Lasers)
For industrial fabrication, the two laser types most commonly used in metal cutting and manufacturing are stimulated gas emission CO₂ lasers and fiber lasers.
Stimulated Gas Emission CO₂ Lasers
The carbon dioxide gas emission laser was one of the earliest lasers invented. Despite the age of the technology, these lasers are still one of the highest power continuous wave lasers available. They’re still frequently used in manufacturing today, and they make a good choice in a lot of applications. As we’ll discuss, assistive gases can be used to adapt the way these lasers work.
Fig. 2: Functional Parts of a CO2 Laser Diagram
From the above diagram, it can be seen quite clearly how the functional parts of a CO₂ laser fit together. Mirrors reflect light into a high intensity monochromatic stream of light photons that exit the laser at the wavelength shown. Water is used to cool the gas tube during stimulated emission. Various gases, such as CO₂, N2 and helium, can be used during the process.
Fig. 3: Rotational-Vibrational Energy in CO2 Laser Stimulated Emission
From the diagram above, it can be seen that within the vibrational energy levels of CO₂, there are rotational sub-energy levels. A mixture of N2 and CO₂ is introduced into the gas cylinder, and the N2 atoms are excited through an electrical pumping system. The excited N2 atoms begin colliding with the CO₂ atoms, and an energy transfer takes place. This causes the CO₂ atoms to enter a higher vibrational energy level.
At this higher vibrational energy level, spontaneous emission occurs, and the CO₂ atoms reduce in vibrational-rotational energy. They then give off some of their energy, which increases the energy and intensity of the incident light.
CO₂ Laser Cutter Benefits Include:
- Cut thicker materials at a wattage equal to other lasers, such as fiber lasers
- Superior finishing (i.e. fewer burrs) when cutting thicker material
Stimulated Gas Emission Laser Cutting Processes
With stimulated gas emission CO₂ lasers, there are two laser cutting processes that are commonly used: Fusion cutting and oxidative cutting. These are based on the use of assistive gases during the cutting process.
- Oxidative cutting uses oxygen as an assistive gas. Oxygen increases heat and the reaction rate at the cutting interface. This, in turn, enables the cutting of thicker material at faster rates. The quality of the surface finish will, however, be reduced.
- Fusion cutting uses reaction inhibiting nitrogen or argon as an assistive gas in the cutting process. This process has the advantage of producing a virtually oxide-free cutting edge.
Fig. 4: Typical Oxidative Laser Cutting of Sheet Metal
Oxidative Laser Cutting with Oxygen as an Assistive Gas
Oxygen is the standard active assistive gas used for laser cutting mild and high carbon steels with CO₂ lasers.
When cutting with oxygen, the chemical reactivity of oxygen at the elevated temperatures under the laser causes the material to be burned with an accelerated action. The burned material is sometimes vaporized if the induced temperature in the vicinity of the laser cut is high enough. The liquid iron oxide of low viscosity is removed from the kerf by the sheer force of the oxygen jet directed into the kerf.
The pressure of the oxygen jet determines the rate of removal of the melt shear from the kerf. The value of the maximum oxygen pressure will be determined by the thickness of the material that will be cut. Oxygen purity is important for quality cutting.
Laser Cutting with Nitrogen as an Assistive Gas
Cutting with non-reactive gases, such as nitrogen, is often referred to as clean cutting or high-pressure cutting. In this case, the material is melted solely by the laser power and blown out of the cut kerf by the kinetic energy of the gas jet.
With nitrogen assisted laser cutting, the melt-shear removal process is the only active process as inert gases do not react with the molten metal to create additional heat. Therefore, much higher laser power and gas pressures are required. This is because molten steel has quite a high viscosity compared with the liquid iron oxide generated during cutting with oxygen.
Laser cutting with nitrogen would be a typical choice for cutting some stainless steels (to avoid part oxidation) as well as aluminum and some of its alloys.
Fiber Lasers
With recent advances in technology and capabilities, fiber lasers are rapidly becoming the laser of choice for industrial cutting applications. A fiber laser is a type of solid-state laser where monochromatic and pumped, intensified light is directed and wave-guided down an optical fiber towards the cutting surface. The light is not passed through any gas for stimulated emission (i.e. a “solid gain medium”).
Fig. 5: Active Components and Beam Propagation in a Fiber Laser
The diagrammatic view below, shows the basic configuration of the optical circuit of a high-power fiber laser. The optical circuit consists of three major sections: The pump section, the oscillator section and the beam delivery section. In the pump section, laser light from pumping laser diodes (LDs) passes through optical fibers into a pump combiner. The pump combiner couples the pump light from the multiple LDs into a single-mode optical fiber.
In the oscillator section, the pump light from the pump combiner propagates through a double-clad fiber (active fiber), as depicted in Fig. 6. The pump light excites the Yb ions and is amplified by the FBGs (Fiber Bragg Gratings). The FBGs act as mirrors with high and low reflectivity. The laser light is emitted from the low-reflectivity FBG. The beam delivery section is composed of an optical fiber that passes the laser light from the oscillator section to a processing head or beam coupler.
Fig. 6: Working Mechanism of a Fiber Laser
Generally, when laser cutting metals with fiber lasers, the upper limit on thickness of metal sheet that can be cut is around 20 – 25 mm for mild steels. Above this thickness, higher power CO₂ lasers are used. However, with specialized fiber lasers that are available for a higher price, it is possible to cut plates thicker than this. Fiber lasers are now the tool of choice for cutting metal below 15mm thickness.
Fig. 7: High Power Fiber Laser Cutting Thick High Carbon Steel Plate
Comparison of Fiber and Co2 Lasers
Fiber and CO₂ lasers are each better suited to certain manufacturing processes. The main benefit that fiber lasers offer is increased efficiency. CO₂ lasers, on the other hand, offer high power and performance. There are a number of considerations with each depending on part type, material, thickness, etc.
A summary of the main benefits associated with each:
Fiber Laser Cutter Benefits:
- More rapid processing times vs CO₂ laser cutting
- Greater energy efficiency (2 to 3 times that of CO₂)
- Greater reliability and performance
- No optics alignment or adjustment
- Reduced maintenance requirements
- The ability to process highly reflective materials like copper and brass
- Ability to cut thinner metals (better wavelength absorption)
- Lower cost per part due to faster, more efficient cutting and simpler machine maintenance
CO₂ Laser Cutter Benefits:
- Cut a wider range of materials (wood, leather, textiles, etc.)
- CO₂ lasers can perform better when cutting thicker materials – they deliver a smoother surface finish and better edge quality when cutting materials above 5mm.
- Cuts thicker materials and feature rich parts faster, with faster piercing
- Good accuracy, with more intricate cutting designs or acute angles possible
Which Type of Laser to Use?
As well as making a choice between fiber and CO₂ lasers, it’s also necessary to consider using fusion or oxidative cutting with a CO₂ laser.
The main factors that influence the choice of laser cutting technology and process are the type, thickness and light reflectivity of the material being cut. An additional complication is oxidation in the case of O₂ assisted CO₂ laser cutting.
Below is a table illustrating the compatible laser cutting technologies for various materials:
Type of Laser / Material to be Cut | CO2 | CO2 NITROGEN ASSIST | CO2 O2 ASSIST | FIBER LASER |
---|---|---|---|---|
Carbon Steel | ✓ | ✓ | ✓ | |
Stainless Steel | ✓ | ✓ | ||
Copper | ✓ | ✓ | ✓ | |
Aluminium | ✓ | ✓ | ✓ | |
Titanium | ✓ | ✓ | ✓ | |
Plastic | ✓ | ✓ | ||
Glass | ✓ | |||
Paper | ✓ | |||
Wood | ✓ | |||
Stone | ✓ |
Table 1: CO₂ vs. Fiber Laser Cutting: Material Comparison
When to choose a fiber laser?
Fiber is generally the default choice for most laser cut parts simply due to speed, cost and ease of operation.
- Thinner material (5-6mm or below)
- Cost sensitive parts
- Parts with standard features, no very acute angles
When to consider a CO₂ laser?
- Cutting non-metallic materials
- Cutting very thick metals (6mm or above)
- Exceptionally acute angles or complex features
What Materials Can Be Laser Cut?
One of the big general benefits of laser cutting is that lasers can be used to cut a wide variety of materials. It is necessary to select the right laser and cutting process for each material. However, lasers can be used on more materials than people sometimes expect.
Here are the materials most often cut with laser cutters:
Metals
Lasers are particularly useful for cutting metals. Not only can lasers cut most metals, but they also create accurate, clean cuts in metal. On top of this, lasers can cut metals quickly and at a relatively low cost. Lasers can also be used to cut both thin and thick metals, with high power CO₂ lasers being used for the thickest metals.
Metals that are commonly cut with lasers are:
- Mild steel
- Cold rolled steel
- Stainless steel
- Steel alloys
- Iron
- Aluminum and aluminum alloys
- Brass
- Copper and copper alloys
- Titanium and titanium alloys
The biggest challenge when it comes to laser cutting metals is cutting highly reflective metals. Brass and copper can be challenging to cut, although fiber lasers tend to be effective. Other highly reflective and difficult to cut metals are gold, copper, silver and bronze.
Plastics
CO₂ lasers can be used to cut plastics, although only certain types of plastic can be cut with lasers. Fiber lasers can be used to mark plastic parts, but cutting is not recommended. The working environment also needs careful consideration because many plastics may produce toxic fumes when laser cut.
- Acrylic, PMMA and Lucite - Acrylic, PMMA and Lucite are see-through plastics that all suit laser cutting very well. When cut, these plastics produce a clean finish at the cut edge. Toxic fumes can be produced when cutting these materials, so good ventilation is needed. Low power CO₂ lasers are usually used for cutting these plastics.
- PolyOxyMethylene (POM) - This plastic is used in engineering applications when strength, chemical resistance and dimensional stability are required. Gears and guiding and sliding elements are common applications for POM. This plastic, as with acrylic, PMMA and Lucite, cuts cleanly under a CO₂ laser, producing a good finish. Again, low power lasers are best, and ventilation is required.
Wood
It is possible to cut wood with a laser, although attention needs to be paid to flammable resins. Plywood and MDF are two common types of wood that are suitable for laser cutting.
- Plywood - Plywoods can be cut with lasers, although high-power lasers are needed and cutting needs to be performed quickly to reduce burns along the cutting edge. Both CO₂ and fiber lasers can be used for wood, though fiber lasers are used for marking rather than cutting. Ventilation is required because resins used to bond the layers of ply together produce toxic fumes.
- Medium Density Fiberboard (MDF) - MDF is more difficult to cut than plywood, although it is possible to laser cut MDF. The reason for the difficulty is the high density of the material and the high adhesive content. Again, high power lasers and fast cutting processes are required. Staining and soot marking is common with MDF. Again, ventilation is required because MDF produces toxic fumes when laser cut.
Paper and Cardboard
Paper and cardboard can both be cut with a laser.
It’s possible to get very good results when laser cutting these materials, with intricate patterns achievable. Decorative, pop-out cards are an example of a cardboard laser cutting application. Moderate power levels and fast speeds should be used for cardboard, and low power levels and fast speeds should be used for paper. Ventilation is required because toxic fumes may be produced.
Leather
Leather can be laser cut. CO₂ lasers are most often used, with cutting through multiple passes often being a good method. Clean cuts are possible when laser cutting leather, and it’s possible to avoid problems associated with other cutting methods.
Ceramics
Ceramics are ideal for laser cutting because they have good thermal insulation properties. Ceramics cut with a clean edge under a laser and little discoloration usually takes place. Most commonly, CO₂ lasers are used, with careful selection of lasers and processes necessary. Laser engraving is also common with ceramics, with lasers being used to create a shallow engraved texture.
Some types of ceramic that are laser cut are alumina, porcelain, zirconia, earthenware, silicon carbide, aluminum nitride and ceramic tiles.
What Materials Cannot Be Laser Cut?
Here are some materials that can’t be cut with a laser.
Some Plastics
While some plastics can be laser cut, others can’t. Most of the materials that can’t be laser cut are plastics. Here are some common plastics that it isn’t possible to cut with a laser:
- Polyvinyl Chloride – High concentrations of acids and toxic fumes are produced when this material is laser cut. These can be dangerous and can also damage the laser cutter.
- Polycarbonate – Very thin sections of this material can be laser cut. However, it tends to discolor badly or burn under a laser when thicker sections are cut.
- High Density Polyethylene (HDPE) and Acrylonitrile Butadiene Styrene (ABS) – These plastics melt too readily when laser cut, resulting in poor quality cuts. ABS also produces toxic fumes, including cyanide, methyl styrene, phenol, phenyl cyclohexane and benzene derivatives.
Fiberglass
Fiberglass consists of glass and epoxy resin, which are materials that both perform poorly when laser cut. Glass is highly reflective and difficult to laser cut, while epoxy resin creates a large number of toxic fumes. Those fumes include hydrogen cyanide, H2, CO, CH4, C2H6, C2H4, C3H6 and C3H8, ethane, ethylene, propylene and propane.
Another material that can’t be cut because of the presence of epoxy resin is coated carbon fiber. This is carbon fiber that’s been pre-impregnated with epoxy resin so it can be thermally bonded in a hot press.
Polystyrene and Polypropylene Foam
These materials are generally regarded as being too flammable to be laser cut. They are often burn or become misshaped at the cutting edge. Discoloration also occurs.
However, it should be pointed out that nowadays these foams are actually cut with lasers more often. While the high flammability does often rule out laser cutting, with the right lasers and methods, some manufacturing facilities are able to laser cut these materials. Thinner sections of polystyrene and polypropylene foam are more suitable for cutting.
Advantages of Laser Cutting Over Other Cutting Technologies
Laser cutting offers many advantages over other cutting technologies such as mechanical die punching, saw cutting, plasma cutting, waterjet cutting and stamping.
Some of the key advantages are listed below:
- A wide variety of materials can be cut
- Narrower kerf widths
- Less material distortion and a reduction in the heat affected zone
- Higher cutting precision
- High levels of repeatability and rapid iteration during production
- Less material contamination
- Improved safety conditions for operating personnel
- Higher quality cutting edges and little secondary finishing required post cut
- Less material wastage due to superior sheet utilization
- Easier set up makes small lot sizes possible
Repeatability
Laser cutting machines are CNC controlled, and they’re generally operated using complex software to optimize part path, machine speed and sheet metal utilization. This means they produce complex, precision parts in a repeatable and efficient manner. Part variability between production runs is minimal, especially when using a fiber laser machine due to much lower levels of required maintenance.
Finishing
Laser cutting produces generally high-quality cuts and edges for thinner parts, which means costly secondary finishing or cleaning usually isn’t required.
Post-cutting tooling often isn’t required as well, as it often is with other processes like stamping. As well as the cost and time associated with the tooling process, tools don’t need to be maintained or checked for deviation as much.
A reduced amount of contamination of workpiece cutting edges also occurs.
Fig. 8: Laser Cut Parts With Surface Finishing
Higher Precision and More Design Possibilities
Certain part geometries or designs are also possible via laser cutting that could not be made by other methods. Precision is generally better due to less wear and fewer moving parts involved in the cutting process.
Better Sheet Utilization
Fiber lasers in particular have a very focused beam, which reduces kerf width and the amount of material used. Combined with the lower levels of mechanical distortion involved in the cutting process, tighter tolerances, and less material distortion, this means parts can be nested extremely close together on sheet metal being processed by laser cutting. This translates to higher material utilization and lower part cost.
Advantages | Laser Cutting | Mechanical Cutting | Waterjet Cutting | Plasma Cutting |
---|---|---|---|---|
Precision/Tolerances | ✓ | |||
Intricate Design Capabilities | ✓ | |||
No Mechanical Distortion | ✓ | |||
Material Costs (Less Waste) | ✓ | |||
Maintenance Costs | ✓ | ✓ | ||
Quick Prototyping/Design Adjustments | ✓ | ✓ | ||
Composite/Multi-layer Material | ✓ | |||
Thick Materials | ✓ | ✓ | ✓ | ✓ |
No Thermal Distortion | ✓ | ✓ | ||
Operational Costs | ✓ | ✓ | ||
Range of Suitable Materials | ✓ | ✓ | ||
Turnaround | ✓ | ✓ | ✓ |
Disadvantages of Laser Cutting
Laser cutting does have some disadvantages vs other fabrication techniques, and these include:
- Material may exhibit some hardening or appearance changes
- Not all materials are suitable for laser cutting
- Maximum thickness of 25mm with fiber laser cutters
- Higher energy and power consumption
- High equipment costs
- Burrs or coarse edge finishing on thick parts may require secondary finishing
Material Limitations
Laser cutting can be used on a variety of metallic and non-metallic materials. However, laser cutter types and the assistive gases impose some limitations with certain materials.
Material Thickness
Additionally, the thickness of materials that can be cut is limited with laser cutting. Thicker materials can also exhibit a higher incidence of edge micro-burrs and other issues.
- The upper limit on thickness when cutting metal with a fiber laser is around 25mm
- The upper limit on thickness when cutting metal with a CO₂ laser is around 70mm
In comparison with plasma cutting, laser cutting for metals is generally more precise and uses less energy. However, most industrial lasers cannot equal a plasma cutter’s capabilities with metal parts of higher thickness.
Material Hardening
The hardening of laser cut edges due to processing may be problematic in some applications. Parts requiring further processing, such as powder coating or painting, may need intermediary processing following laser cutting before it can take place. The addition of this step increases both the turnaround time and total processing costs.
When to Use Laser Cutting?
Laser cutting makes a great choice in a number of different manufacturing scenarios. The main benefits it brings are speed and accuracy, but there are other upsides as well.
Below are the situations in which it could well be a good idea to employ laser cutting.
When a High Level of Precision is Needed
It’s possible to achieve the highest levels of precision with laser cutting. Laser cutters are highly accurate, and they produce very narrow kerf widths. Kerf widths as small as 0.1mm are possible with laser cutters. With computerized controls, very accurate cuts can be made, and the possibility of human error is removed from the equation.
Laser cutting is particularly good for delicate and complicated cutting patterns or where precision is important in the function of a component part. Precision can also be repeated across a large number of parts with laser cutters. If consistency is important in production, then laser cutting might be the best option.
To Achieve High Quality Cut Edges
The quality of the finish at the cut edge when cutting with a laser does depend on the material that’s being cut and the laser and cutting process being used. However, under the right conditions, it is possible to create very smooth, burr-free cuts with laser cutters. With other cutting methods, finishing processes are often needed to achieve the same finish qualities.
Not only are better results achieved, but costs can be reduced, and time can be saved as well by avoiding further processing.
When Speed is Important
Laser cutters are great for one-off jobs, such as prototypes or design validation productions, and low to medium volume production runs. With computer assisted cutting, it’s often possible to begin production at very short notice. Equipment set up procedures that are needed with other methods are avoided, and production can begin very quickly.
Laser cutters can also be faster than other cutting methods over the course of an entire production run. If it’s important to complete a large production quickly, depending on the part being produced, it will often be quicker with laser cutting.
To Be Environmentally Friendly and for Safe Working Conditions
Laser cutters can be used for environmental and safety reasons.
While laser cutters themselves use a large amount of power, the entire laser cutting production process is often more environmentally friendly than other methods. Other stages associated with methods such as saw cutting and die punching can mean extra processing is required. This all contributes to power usage as well as the consumption of resources like water for cleaning.
There is also less material wastage with laser cutting. Computer aided design (CAD) design systems find the most efficient cutting methods, and this helps to reduce waste.
Laser cutting is also safer for the operatives at a production facility. Laser cutting takes place behind sophisticated guard systems. Cutting processes are also designed to be highly safe, making it much less likely that workers will be injured during production.
To Avoid Issues Associated with Other Cutting Methods
Laser cutting can be used when other cutting methods create problems.
If contamination is an issue, for example, laser cutting will help to avoid this. Contamination may occur at the cutting edge of certain materials with saw cutting, for example. Other cutting methods might cause different problems as well. In leather, for example, laser cutting can be used to avoid distortion issues that other cutting methods cause.
Where Are Laser Cut Parts Used?
Due to the low set-up costs, rapid turnaround, low and medium-volume production flexibility, laser cut parts are widely used in a number of fields and applications.
Applications where laser cutting is common include:
- Automotive parts
- Aerospace
- Recreational vehicles
- Medical products
- Consumer electronics
- Furniture
Taking the automotive industry as an example, lasers can be used to cut interconnecting parts on most of the chassis, to carry out hydroformed part secondary processing or even to create air bags.
Laser cutting is often done with metal component parts, as these can pose a challenge for mechanical cutting or stamping. Large-scale production of parts made from plastic and other materials is also possible with laser cutting. However, this is less common, because laser cutting has certain limitations compared to certain fabrication technologies, such as plastic injection, for non-metallic parts.
Sales of laser cutting machines have increased on average 10% per year in a number of recent years. This tracks with the increased performance of laser cutting machines and technology vs the alternatives in the market.
Fig. 9: Automotive Industry's Dominance in Laser Cutting Technology Market
Conclusions
- The practice of using lasers as a tool to cut and shape materials, and especially metals, is a practice of choice in plenty of industries.
- The reason for this is the high level of precision and repetitive procedural accuracy that is obtainable with CNC laser cutting.
- Although it is possible these days to use laser cutters to machine thick metal or steel plates, the optimum sheet metal thickness to cut using laser cutters is below 20mm.
- The type of material to be cut will determine which type of laser it is best to use.
- Generally, fiber lasers are becoming the cheapest and most effective laser cutters on the market today. Historically, however, CO₂ lasers have been used for most metal cutting applications.
If you have any unanswered questions on sheet metal laser cutting, please follow the suggested links in this document to our proprietary literature. This provides a wealth of information on a range of engineering and production topics. Or explore our corporate website: komaspec.com.
Komaspec’s Sheet Metal and Laser Cutting Services
Komaspec’s in-house sheet metal and laser cutting capabilities, and our proprietary laser cut quotation and DFM engine, along with our extensive experience in manufacturing laser cut parts in our China sheet metal facility, enables innovative companies to develop new and complex products quickly and cost effectively. Laser cutting can turn around parts in days rather than weeks and has impressive levels of precision and repeatability.
KOMASPEC'S PRECISION LASER CUTTING
Transform your engineering projects with our advanced laser cutting technology. Achieve unmatched precision and quality.